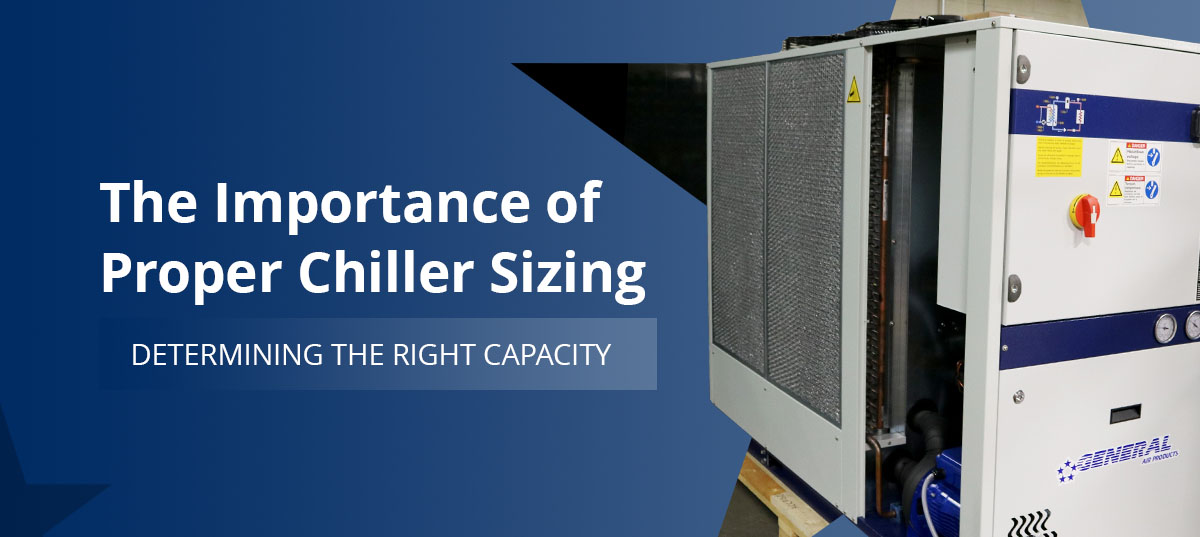
Chillers are critical for keeping products, equipment, materials, and ingredients at proper operating temperatures. You’d be surprised how heavily your chiller’s size can impact performance, energy consumption, and operating expenses. Choosing an ill-suited size for your business can compromise system performance and efficiency.
But how do you determine the right chiller size for your workflow and facility, and why is it important?
The Importance of Chiller Sizing
Size is essential when choosing a chiller for your facility’s cooling needs. While sizing up to increase cooling capacity may seem like the clear route, it can actually be counterproductive.
Chillers are designed for gradual temperature reduction. If your device’s cooling capacity is too large, your tank’s temperature could drop too quickly. An oversized chiller can cause overcooling, which can:
- Drive the coolant temperature below the desired range.
- Decrease energy efficiency.
- Impede system performance and operation.
You’ll also spend more upfront than necessary, and your operating costs will rapidly snowball. But undersized chillers aren’t off the hook — they pose their own set of risks. A chiller that’s too small will struggle to meet your building’s cooling requirements. It can’t sufficiently stabilize water temperature, causing inadequate airflow and cooling capacity.
Whether a chiller is too large or compact, it usually can’t run at peak efficiency. Correctly sizing your device is key to optimizing performance, productivity, and capital savings.
Factors Affecting Chiller Sizing
Numerous factors can help you determine accurate load calculations, cooling requirements, and chiller size. These include:
- Your facility’s cooling load profile, such as hourly, daily, weekly, or monthly.
- The heat generated by your equipment, space, and operations.
- The type of equipment you’re using.
- Thermal properties of fluids and materials.
- Surrounding equipment temperatures.
We’ll examine a couple of these factors below to see how they affect chiller sizing.
1. The Type of Fluid
The type of fluid your chiller uses can play a crucial role in the size selection process. Consider the fluid’s boiling point, freezing point, and viscosity level. These factors can help you ascertain its performance in different environments.
For example, water is often ideal for fluid temperatures above 4 degrees Celsius due to its strong thermal properties. In lower temperatures, however, water will come very close to or drop below the freezing point. In that case, a water and glycol mixture is better for your chiller.
Additionally, think about the fluid’s performance in terms of the chiller’s long-term stability. A corrosion inhibitor can protect the device’s metallic elements from premature degradation. If your current fluid cannot contain this inhibitor, you’ll likely need to use a different fluid.
2. Ambient Air Conditions
Surrounding temperatures can directly impact chiller performance. As ambient wet or dry bulb temperatures climb, the condensing temperature also rises. This process increases the chiller’s power consumption.
Ambient air temperature also influences other equipment components, like pumps, compressors, motors, and electronics. Excess ambient temperatures and heat produced during operation can strain your equipment, reducing the life span of these mechanisms.
For this reason, you should consider the highest temperature at which these chiller parts can function properly. Your building’s geographical location and seasonal temperature fluctuations will also impact ambient temperatures.
Steps to Determine the Appropriate Chiller Size
Calculating chiller capacity will help you identify the correct size for your business. You can use the steps below as a guide.
1. Determine Your Total Heat Load
The total heat load is the amount of heat that needs to be removed in order to maintain the optimum temperature. Factors like the thermal output of any machinery or equipment, insulation, and the size of the space all factor into the total heat load.
2. Calculate British Thermal Units (BTU) per Hour
BTU is a unit of measurement that indicates a device’s cooling power. It calculates the amount of heat removed from a space within one hour. Typically, a higher BTU translates to a more powerful chiller and cooling abilities. Achieving the right BTU-to-space ratio is important for proper cooling and chiller efficiency.
3. Find the Chiller’s Cooling Capacity
Cooling capacity — which is measured in refrigeration tons for industrial chillers — determines the cooling system’s ability to remove heat. One refrigeration ton equals 12,000 BTU per hour and refers to the capacity needed to freeze water to 32 degrees Fahrenheit.
4. Establish the Proper Chiller Size
To figure out the chiller cooling capacity that you need, divide the BTU per hour by 12,000 BTU. The resulting number indicates the most suitable chiller size for your facility and operations.
Industrial Chiller Systems Available at General Air Products
Industrial chillers fulfill many manufacturing applications. Whether you work in pharmaceuticals, food processing, welding, printing, or another industry, General Air Products is ready to help you find a high-quality product for your facility. We have a broad inventory of industrial chiller solutions available, including:
1. Air-Cooled Chillers
We have standard and custom air-cooled water chiller models. Each provides multiple configuration options to accommodate your facility’s existing layout. These chillers range in cooling capacities from less than 1 ton to 90 tons. We also have air-cooled chillers for various industries, like medical facilities and breweries.
2. Water-Cooled Chillers
We also carry a full line of standard and custom water-cooled chillers. These tanks range from 1 to 60 tons. They’re engineered from durable materials like stainless steel for lasting performance. Our water-cooled chillers consistently output fluids at 45-degree Fahrenheit temperatures. They also have many other features, such as:
- Microprocessor controllers
- Stainless steel or brazed plate evaporators
- Suction accumulators
- Water flow switches
- Control circuit fusing
3. Fluid Coolers
Our fluid cooler systems help keep your industrial equipment cool and prevent harmful sludge buildup. You can choose from a standard assortment of fluid coolers or develop a custom solution for your unique cooling needs.
To resist corrosion and thermal wear, these coolers are constructed with:
- High-efficiency coils
- Copper tubes
- Aluminum fins
- Galvanized steel housing
They also include direct-drive propeller fans for quick, balanced air distribution. Feel free to browse our fluid cooler manual for a complete rundown of our fluid cooler models, customization options, and technical details.
Find the Ideal Chillers and Cooling Products for Your Facility Today
Your business needs consistent, reliable cooling power to optimize energy use and minimize utility costs. Explore our selection of chillers, cooling capacities, and dimensions to determine the right fit for your space. If you need assistance in choosing the right chiller type and size, please contact our team anytime!