At General Air Products, we are often asked, “Should I Use Nitrogen or Dry Air in freezer rooms and cold storage sprinkler systems?” Our answer – as a manufacturer of nitrogen generators, dry air generators and air compressors – is dry air. Every time.
There are three technologies available for filling dry pipe and pre-action sprinkler systems – standard compressed air, dry air generators – such as the Dry Air Pac® – and nitrogen generators. General Air Products is the only company in the fire sprinkler industry that manufactures all three of these types of equipment. This puts us in a unique position to speak to the pros and cons of each technology given a specific application. So, the first thing to take away here is that all of these products – compressors, dry air generators and nitrogen generators – have positives and negatives when applied to a dry pipe or pre-action system in any type of building.
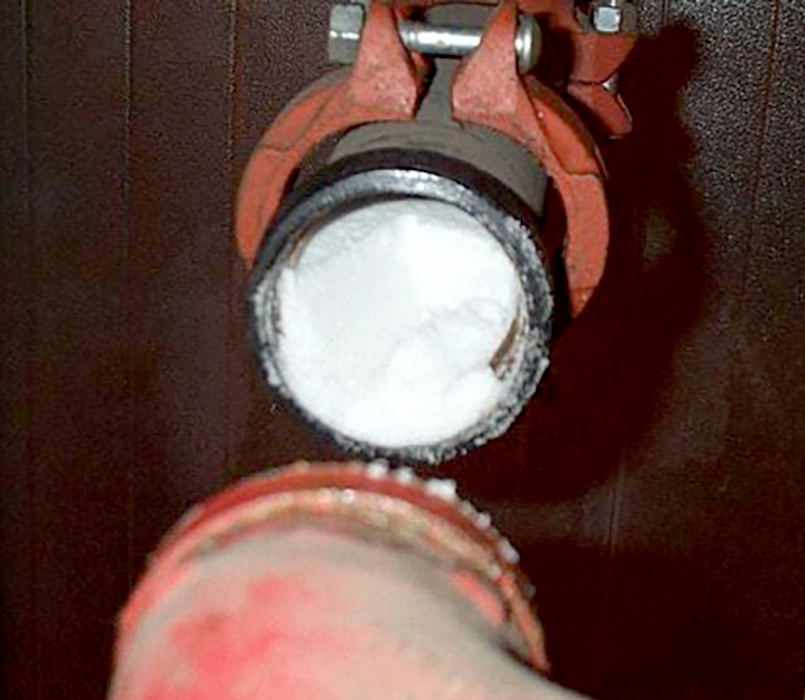
Choosing Your Cold Storage and Freezer Room Air Supply
Let’s start with the easy one – never use standard compressed air in a freezer room application. When you compress air you also draw in water vapor from the humid ambient air – this vapor collects as liquid water in the tank and some of it continues downstream as vapor. Any water or water vapor sent downstream from the fire protection air compressor in a freezer room system will freeze at the length of pipe that is at the interface of the freezing and ambient area.
(Note that pulling air from the freezer room and then through the compressor does not change this as any air pulled through an air compressor will be heated up in the process. As this water vapor freezes it will not take long to turn into a sizable ice plug. For this reason, standard compressed air should never be used in a freezer room or cooler.)
(ALSO NOTE: A poorly maintained dry air generator (Dry Air Pac®) or a poorly maintained nitrogen generator will cause ice plugs to form in freezer rooms, just like an standard air compressor!)
So, we are left with a choice between dry air or nitrogen.
Where is the Corrosion in the First Place?
Though both dry air and nitrogen have been proven to mitigate corrosion in dry systems, the thing to remember here is that freezer rooms and cold storage fire sprinkler systems are not prone to corrosion. For corrosion to take place, liquid water in the pipe is required. With both dry air and nitrogen generators, we’re allowing virtually no moisture into the system, and the lack of frequent hydrostatic flow testing leaves us with minimal liquid water ever being introduced.
Typically, a hydrostatic flow test is done at the commissioning of a dry pipe or pre-action system and then performed annually. This is not the case with most cold storage systems. While the initial hydrostatic test is required, allowances are made for freezer and cold storage sprinkler systems that this test does not have to be performed by running water through the entire system every year – to do so would require the freezer to be turned off each time. Cold storage facility managers will avoid this at all costs.
If we are not introducing liquid water to the system and the piping system sits in an environment where liquid water cannot exist, then there is little to no cause for concern with corrosion.
Dry air generators are dramatically less expensive than nitrogen generators in systems larger than 1000 gallons in capacity. If there is little cause for corrosion in a sprinkler system then why should you opt for the more expensive option of nitrogen? This point alone makes dry air the optimal choice, though there are several more to consider. General Air Products still recommends a dry air generator even in the few instances where a nitrogen generator is less expensive – this has to do with the performance of each unit type over time.
Nitrogen Generators are very susceptible to dry system leak rates
One of the biggest issues with nitrogen generation is the lack of supervisory gas flow. In the chart below you can see how dramatically air flow from the compressor is reduced when it goes through a nitrogen membrane versus going through the dry end of a dry air generator like the Dry Air Pac®, or when it is not filtered at all as in a fire protection air compressor. This is a big problem with nitrogen generators in fire sprinkler systems as a whole, but it is of paramount importance in freezer room applications.
What the diagram tells us is that a fire protection air compressor has the best supervisory gas flow and can keep up with extreme leak rates. This is because air compressors and dry air generators are sized for 30-minute fill requirements whereas a nitrogen generator that is generating 98% nitrogen is only sized for system maintenance. There has been no real discussion on the leakage rates of dry air pre-action systems over that past many years – air compressors can keep up with them. The reason we need to discuss them now is that nitrogen generators cannot.
Air leaks in dry and pre-action sprinkler systems will always grow over time. While maintaining 98% nitrogen in a sprinkler system will severely limit the amount of corrosion that takes place, it will not slow all of the other causes of air leaks in sprinkler systems.
Keeping all of this in mind, let’s apply a nitrogen generator to a freezer room…
Upon install in a newly commissioned sprinkler system a properly sized nitrogen generator should keep up with system demands for pressure (at 98% nitrogen). Time passes, forklifts shake the shelving that contains the in-rack sprinkler system causing permanent leak points to form at threads and couplings. Gaskets dry rot, valves don’t seat properly and all the other day-to-day things occur that cause leaks.
The nitrogen generator, due to its inherently reduced flow, is running more and more each day to keep up with the pressure loss. Before long, it cannot keep up, and a run time or low-pressure alarm is triggered.
In most cases, when a nitrogen generator can no longer keep up with the demands of the system you can turn it to air mode and then hunt down all of the air leaks so that you can get it back into nitrogen mode again. A costly and painstaking process in any system, but in a freezer room or cold storage warehouse sprinkler system, it is nearly an impossible one without shutting down the freezer room.
Ask your service manager about the techniques used to find leaks – spraying soapy water, introducing mint scent – then ask about using those techniques in a freezing environment.
Referring back to the diagram, you can see the difference between the flow rate of a nitrogen generator and that of a dry air generator – and it is substantial – meaning the need to find and address these leaks will be substantially less with a dry air generator. It can keep up.
The Best Solution: Dry Air Pac®
General Air Products’ Dry Air Pac® has been dutifully serving as the air supply in freezer room and cold storage fire sprinkler systems for over 25 years and the issues mentioned here are why it works where other technologies run into costly struggles and freezer room down-time. In addition, dry air is almost always a lower cost solution than a nitrogen generator.
As mentioned in the beginning of the article, all of these technologies have pros and cons. Standard compressed air is the least expensive but does contribute to corrosion to varying degrees. Nitrogen generators reduce corrosion best where there are large amounts of standing water in the fire sprinkler system, and dry air generators are best applied where there are small amounts of standing water, such as in freezer rooms. Both nitrogen and dry air generators are maintenance intensive – filters must be changed or the units will not perform as designed. In the case of our Dry Air Pac®, one additional step is necessary – the desiccant needs to be changed every 3 years. Dry air can also serve more systems than a nitrogen generator – regardless, we recommend no more than 3 systems per air supply device, not matter which you choose.
It is for all of these reasons that we definitively tell our customers that they should use a dry air generator on their cold storage or freezer room dry pipe sprinkler systems. Every time.
And now, we’ve made Dry Air Pac® even better.
Introducing the Dry Air Pac® Advance Series.
The new Advance Series is the most reliable, efficient, and user-friendly dry air solution we’ve ever offered. With upgraded desiccant towers for improved moisture removal, an intuitive digital control panel, and easy-access push-connect fittings for simplified maintenance, the Advance Series is purpose-built to handle the demands of freezer rooms and cold storage fire protection systems.
Learn more here.